Gear oil pump series
High viscosity pump series
Centrifugal pump series
Pump series for other purposes
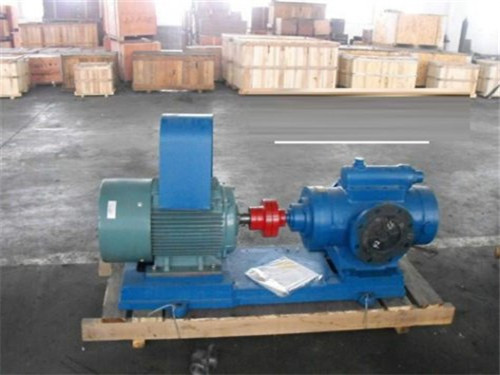
3G series screw pump
Introduction to the 3G series screw pump:
It is used to transport media with a temperature ≤ 150 ℃, viscosity of 3-760cSt, no solid particles, no corrosion, and lubricating properties
Applicable pressure range: 0.6-2.5MpaApplicable flow range: 0.6-123m3/hMainly used in fuel transportation, hydraulic engineering, shipbuilding engineering, petrochemical and other industries1. The medium is continuously transported in a straight line, without stirring or pulsation2. Low vibration and low noise3. High pressure4. Simple structure and convenient disassembly and assembly5. Small size and light weight6. Slight wear and long service lifeThe structural form of the 3G series screw pump is generally mechanical seal. The pump is driven by an electric motor through a claw type coupling. Rotate clockwise from the extended end of the spindle towards the pump year
Materials of 3G series screw pumps
Main and slave screws 16MnCrS5,40Cr, 45,38CrMoALA
Pump body: HT200, QT450-10, ZCuSn10Pl, ZG270-500
Common troubleshooting methods for 3G series screw pumps
1. Severe vibration or noise in the pump body
Cause: The water pump is not installed firmly or the pump is installed too high;
; Damaged motor ball bearings; The water pump spindle is bent or not concentric or parallel to the motor spindleSolution: Install the water pump steadily or lower the installation height of the water pump; Replace the motor ball bearing; Correct the bent water pump spindle or adjust the relative position between the water pump and the motor
2. Overheating of transmission shaft or motor bearings
Causes: Lack of lubricating oil or bearing rupture, etc
Solution: Add lubricating oil or replace bearings
3. The water pump does not discharge water
The reason for this is that the pump body and suction pipe are not fully filled with water.
; The dynamic water level is lower than the water pump filter pipe; Rupture of suction pipe, etcProcessing method: The sealing surface between the screw and the shell is a spatial curved surface. There are non sealing areas such as ab or de on this surface, and many triangular notches abc and def are formed with the groove part of the screw. These triangular notches form channels for the liquid, connecting the active screw groove A with the grooves B and C on the driven screw. And grooves B and C follow their own spiral and are connected to grooves D and E on the back, respectively. Due to the presence of triangular notches a'b'c 'similar to the front on the sealing surface where slots D, E and F (which belong to the other spiral) are connected, D, F, and E will also be connected. In this way, the groove ABCDEA forms an "∞" - shaped sealing space (if a single head thread is used, the groove will wrap the screw in the axial direction, connecting the suction and discharge ports, and cannot form a seal). It is not difficult to imagine that on such a screw, many independent "∞" - shaped sealing spaces will be formed, and the axial length occupied by each sealing space is exactly equal to the lead t of the accumulated rod. Therefore, in order to separate the oil suction and discharge ports of the screw, the length of the threaded section of the screw should be at least one lead
Five reasons for screw wear in 3G series screw pumps
1. Each type of plastic has an ideal plasticizing processing temperature range, and the barrel processing temperature should be controlled to approach this temperature range.
. Granular plastics enter the barrel from the hopper and first reach the feeding section. Dry friction is inevitable during the feeding section. When these plastics are not heated enough and melt unevenly, it is easy to cause increased wear on the inner wall of the barrel and the surface of the screw. Similarly, in the compression and homogenization stages, if the melting state of the plastic is disordered and uneven, it can also cause accelerated wear2. The speed should be adjusted appropriately. Due to the addition of additives such as fiberglass, minerals, or other fillers to some plastics. These substances often have much greater friction against metal materials than molten plastics. When injecting these plastics, if a high rotational speed is used, it will not only increase the shear force on the plastic, but also produce more torn fibers. The torn fibers contain sharp ends, greatly increasing the wear force. When inorganic minerals slide at high speeds on metal surfaces, their scraping effect is also significant. So the speed should not be set too high3. The screw rotates inside the barrel, and the friction between the material and the two causes the working surface of the screw and barrel to gradually wear out: the diameter of the screw gradually decreases, and the diameter of the inner hole of the barrel gradually increases. In this way, the clearance between the fitting diameter of the screw and the barrel gradually increases as they wear out. However, due to the unchanged resistance of the machine head and splitter plate in front of the barrel, this increases the leakage flow rate of the extruded material when it moves forward, that is, the flow rate of the material from the diameter gap towards the feeding direction increases. As a result, the production of plastic machinery has decreased. This phenomenon increases the residence time of the material in the barrel, causing material decomposition. If it is polyethylene, the hydrogen chloride gas generated during decomposition enhances the corrosion of the screw and barrel4. If there are fillers such as calcium carbonate and fiberglass in the material, it can accelerate the wear of the screw and barrel5. Due to uneven plasticization of the material or the inclusion of metal foreign objects in the material, the torque force of the screw suddenly increases, which exceeds the strength of the screw and causes it to break. This is a type of unconventional accident damage
Series code | Main uses | Performance range | |
Trafficm3/h | Pressure MPa | ||
3G | Transport 3-20oE lubricating oil at temperature≤80℃,Lub oil visc3-20oE;temp≤80℃ | 0.6-570 | 2.5 |
3GR | Transporting 3-50oE heavy fuel at temperature≤120℃,Heavy feul lil visc3-50oE;temp≤120℃ | 0.6-570 | 2.5 |
3Gr | Transporting 1.2-5oE light fuel at temperature≤120℃,Light feul oil visc1.2-5oE;temp≤120℃ | 0.6-570 | 1.6 |
3GW | Transporting high-temperature heating fuel, temperature≤150℃,High temp feul heated oil;temp≤150℃ | 0.6-363 | 1.6 |
3GN | Transporting 100oE high viscosity oil at temperature≤80℃,High visc oil 100oE;temp≤80℃ | 0.6-636 | 2.5 |
Analysis of the Reasons for Sudden Oil Failure of Gear Pump
The sudden inability of the gear pump to suck oil may be caused by various reasons. The fol ...
2025-08-13
Application scenarios and supporting equipment of WCB small electric oil pumping gear pump
WCB small electric oil pumping gear pump is a compact, efficient, and easy to maintain conv ...
2025-08-06
How to find a gear pump manufacturer with guaranteed quality
Finding a gear pump manufacturer with guaranteed quality requires comprehensive considerati ...
2025-07-30
Can gear pumps operate in reverse when transporting liquids
Gear pumps usually cannot be operated in reverse when transporting liquids, for the followi ...
2025-07-23