Gear oil pump series
High viscosity pump series
Centrifugal pump series
Pump series for other purposes
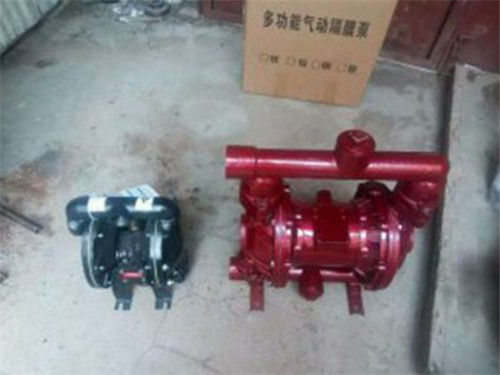
Pneumatic diaphragm pump
Pneumatic diaphragm pump is a new type of conveying machinery that uses compressed air as the power source. It can pump and absorb various corrosive liquids, liquids with particles, high viscosity, volatility, flammability, and highly toxic liquids
Pneumatic diaphragm pumps have four types of materials: engineering plastic, aluminum alloy, stainless steel, and alloy. Pneumatic diaphragm pumps use nitrile rubber, chloroprene rubber, fluororubber, polytetrafluoroethylene, polytetrafluoroethylene, etc. according to different liquid media to meet the needs of different users. Placed in various occasions, it is used to pump media that cannot be pumped by conventional pumps and has achieved satisfactory resultsPneumatic diaphragm pump is a new type of conveying machinery and is currently a new type of pump in China. Using compressed gas as the power source, various corrosive liquids, liquids with particles, high viscosity, volatile, flammable, and highly toxic liquids can be pumped and absorbed completely. There are four types of materials for pneumatic diaphragm pumps: plastic, aluminum alloy, cast iron, and stainless steel. Pneumatic diaphragm pumps use nitrile rubber, chloroprene rubber, fluororubber, polytetrafluoroethylene, and polytetrafluoroethylene according to different liquid media. To meet the needs of different users. Placed in various special occasions, it is used to pump media that cannot be pumped by conventional pumps, and has achieved satisfactory results1. Due to the use of gas as the driving force, the flow rate actively adjusts with the change of back pressure (outlet resistance), making it suitable for medium to high viscosity fluids. The working point of the centrifugal pump is set based on water. If it is used for fluids with slightly higher viscosity, it is equipped with a reducer or frequency converter, which increases the cost, and the same applies to gear pumps2. Use pneumatic pumps in flammable and explosive environments with low cost, such as the transportation of fuel, gunpowder, and explosives, because: 1. Sparks cannot be generated after grounding2. No heat is generated during operation, and the machine will not overheatThirdly, the fluid will not overheat because the pneumatic diaphragm pump has less agitation on the fluid3. In the harsh environment of construction sites, such as the discharge of wastewater from construction sites and industrial mines, due to the high amount of impurities and complex composition in the wastewater, the pipeline is prone to blockage, which creates a high load environment for the electric pump and makes the motor prone to overheating and damage. The pneumatic diaphragm pump can pass through particles and the flow rate is adjustable, and it automatically stops when the pipeline is blocked4. In addition, the pneumatic diaphragm pump has a small volume and is easy to move, does not require foundation, occupies a small area, and is easy to install and economical. Can be used as a mobile material conveying pump5. In the treatment of hazardous and corrosive materials, diaphragm pumps can isolate the materials from the outside world6. Or in some experiments, there are no impurities contaminating the raw materials7. It can be used to transport fluids with relatively unstable chemical properties, such as photosensitive materials, flocculants, etc. This is because the shear force of the diaphragm pump is low, which has little physical impact on the material
Pneumatic diaphragm pump is a volumetric pump powered by compressed air and caused by the reciprocating deformation of the diaphragm. Its working principle is similar to that of a plunger pump. Due to the characteristics of the working principle of pneumatic diaphragm pump, it has the following characteristics:
(1) The pump will not overheat: compressed air is used as the power, and the exhaust is an expansion and heat absorption process. The temperature of the pneumatic pump decreases during operation, and no gas is discharged.
(2) No electric sparks will be generated: Pneumatic diaphragm pumps do not use electricity as power, and grounding prevents static sparks(3) Liquid containing particles can be used: because it operates in a volumetric manner and is a ball valve, it is not easily blocked(4) Low shear force on materials: how to suck in and spit out during operation, so the stirring of materials is small, suitable for the transportation of unstable substances(5) The flow rate can be adjusted by installing a throttle valve at the material outlet(6) It has the function of self suction(7) It can run empty without any danger(8) Able to dive for work(9) The fluids that can be transported range from low viscosity to high viscosity, from corrosive to viscous(10) There is no complex control system, no cables, fuses, etc(11) Small size, light weight, and easy to move(12) No lubrication is required, making maintenance simple and preventing contamination of the working environment due to dripping(13) The pump can always be maintained and will not decrease due to wearThe energy utilization of (14), when the outlet is closed, the pump automatically stops, and there is no equipment movement, wear, overload, or heating(15) There is no dynamic seal, which is easy to maintain and avoids leakage, and there are no dead points during operationPneumatic diaphragm pump is a volumetric pump powered by compressed air, which causes volume changes through reciprocating deformation of the diaphragm. Its working principle is similar to that of a plunger pump. The pneumatic diaphragm pump can be used according to the principles and methods, and according to the instructions and precautions in the specific operating procedures, it can produce important usage effects and contributions, and play a good value in use. When operating a pneumatic diaphragm pump, attention should be paid to the following points: the larger particles contained in the fluid should not exceed the larger particle diameter standard of the pump. Tighten the pump and all connecting pipe joints to prevent static sparks caused by vibration, impact, and friction in the split pump. Use hoses. To periodically inspect and test the integrity of the grounding system, it is required that the grounding resistance be less than 100 ohms. Maintain good exhaust and ventilation, and keep away from flammable, explosive, and heat sources. The intake pressure should not exceed the higher allowable operating pressure of the pump. Compressed air above the rated pressure of the pipeline pump may cause personal injury, property damage, and damage to the pump's performanceStatic sparks may cause explosions, resulting in personal injury and property damage. Use wires with sufficient cross-sectional area as needed and properly ground the grounding screw on the pump. The grounding requirements comply with local laws and regulations as well as some on-site requirements. The exhaust of the pump may contain solids. Do not point the exhaust port towards the work area or people to avoid personal injury. When the diaphragm fails, the material conveyed by the sewage pump will spray out from the exhaust muffler. The pipeline system with pump pressure can withstand the high output pressure achieved, and the multi-stage pump drives the cleanliness and normal working conditions of the pneumatic system. When transporting flammable and toxic fluids, please connect the discharge port to a place far away from the work area. Please use at least 3/8" A smooth inner wall pipeline connects the exhaust port and mufflerThe high pressure of the fluid may cause serious personal injury and property damage. Please do not perform any maintenance work on the pump and material pipeline system when the pump is pressurized. If the rotor pump needs to be repaired, first cut off the pump's intake, open the bypass pressure relief mechanism to relieve the pressure of the pipeline system, and slowly loosen the connected pipeline joints. For toxic fluid pumps and fire pumps, please do not send the pump directly to the manufacturer for repair. The liquid conveying part of the pump is made of aluminum alloy material. Please do not use it to transport liquids containing Fe3+and halogenated hydrocarbons and other halogenated hydrocarbon solvents, as corrosion may cause the pump body to burst. All components in contact with the conveying body will not be corroded or damaged by the conveyed fluid. All operators are familiar with the operation and use of the pump, and are familiar with the precautions for using the pump. If necessary, protective equipment should be provided. Use the pump correctly and do not allow prolonged idle operation
Head M
Model | Traffic M/h | Outlet pressure Kgf/cm | Suction lift M | Great permission By particles φ (mn) | Atmospheric supply pressure Kgf/cm | Large air Consumption M/min | |
QBY-10 | 0~0.8 | 0~50 | 6 | 5 | 1 | 7 | 0.3 |
QBY-15 | 0~1 | 0~50 | 6 | 5 | 1 | 7 | 0.3 |
QBY-25 | 0~2.4 | 0~50 | 6 | 7 | 2.5 | 7 | 0.6 |
QBY-32 | 0~6 | 0~50 | 6 | 7 | 4.0 | 7 | 0.6 |
QBY-40 | 0~8 | 0~50 | 6 | 7 | 4.5 | 7 | 0.6 |
QBY-50 | 0~12 | 0~50 | 6 | 7 | 8 | 7 | 0.9 |
QBY-65 | 0~16 | 0~50 | 6 | 7 | 8 | 7 | 0.9 |
QBY-80 | 0~24 | 0~50 | 6 | 7 | 10 | 7 | 1.5 |
QBY-100 | 0~30 | 0~50 | 6 | 7 | 10 | 7 | 1.5 |
Analysis of the Reasons for Sudden Oil Failure of Gear Pump
The sudden inability of the gear pump to suck oil may be caused by various reasons. The fol ...
2025-08-13
Application scenarios and supporting equipment of WCB small electric oil pumping gear pump
WCB small electric oil pumping gear pump is a compact, efficient, and easy to maintain conv ...
2025-08-06
How to find a gear pump manufacturer with guaranteed quality
Finding a gear pump manufacturer with guaranteed quality requires comprehensive considerati ...
2025-07-30
Can gear pumps operate in reverse when transporting liquids
Gear pumps usually cannot be operated in reverse when transporting liquids, for the followi ...
2025-07-23